Automated welding is a modern manufacturing process where welding operations are carried out using machines, robotics, and control systems with minimal human intervention. This technology ensures faster production, consistent weld quality, and improved safety, making it ideal for industries such as automotive, aerospace, shipbuilding, and construction.
Key Benefits of Automated Welding:
Increased Efficiency: Automated systems can work continuously with high speed and precision, significantly reducing production time.
Consistent Quality: Robotic welders deliver uniform, repeatable welds that meet strict industry standards.
Improved Safety: Automation minimizes human exposure to hazardous fumes, heat, and sparks.
Cost-Effective: Reduces labor costs and material waste over time through optimized workflows and fewer errors.
Why Choose Automated Welding?
Whether you're looking to scale up production or improve quality and safety, automated welding offers a reliable, high-tech solution to meet modern manufacturing demands.
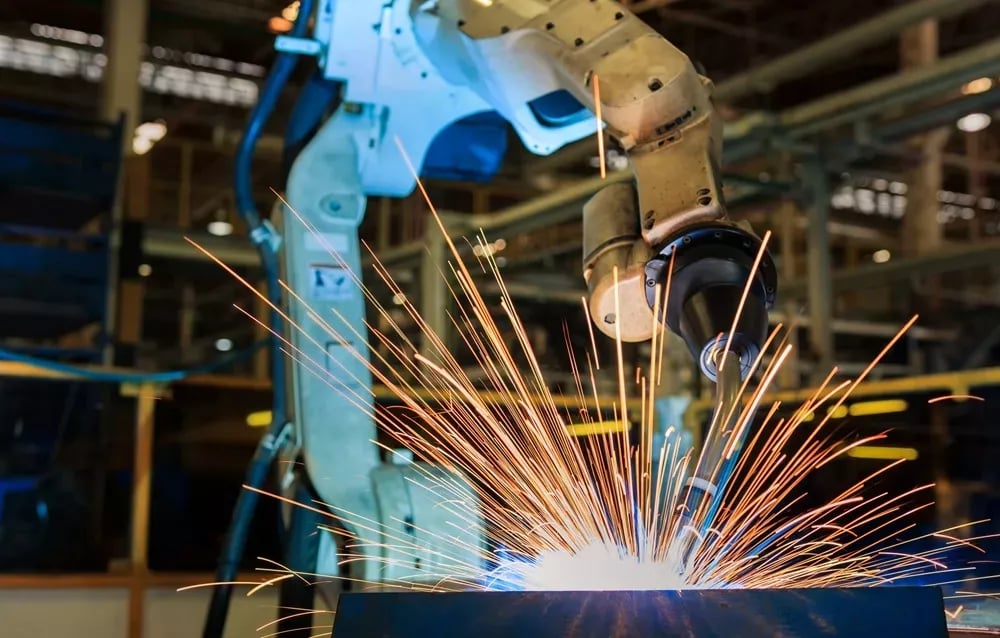
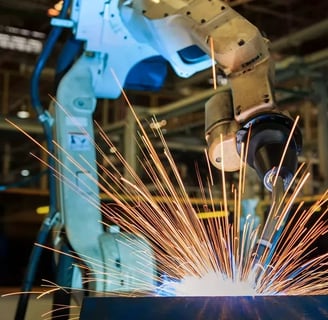
MIG:
MIG welding (Metal Inert Gas welding), also known as Gas Metal Arc Welding (GMAW), is one of the most popular and versatile welding methods used in modern fabrication. It involves feeding a continuous solid wire electrode through a welding gun into the weld pool, while a shielding gas protects the weld from atmospheric contamination. Known for its speed, ease of use, and clean results, MIG welding is ideal for both thin and thick materials, including steel, stainless steel, and aluminum. Whether for automotive repairs, industrial fabrication, or home projects, MIG welding offers strong, reliable joints with minimal cleanup and high efficiency.
SPOT:
Automated spot welding is a manufacturing process that uses robotic systems or automated machinery to join two or more metal sheets at specific points, known as "spots." This technique is widely used in industries such as automotive, aerospace, and appliance manufacturing due to its speed, precision, and efficiency. In this process, metal sheets are accurately positioned using robotic arms or fixtures. Electrodes then press the sheets together and deliver a high electric current through the contact point. The resistance to the current generates heat, causing the metal to melt and fuse at that spot. Once cooled, a strong and durable weld is formed. The system then moves to the next location to repeat the process. Automated spot welding offers several advantages including consistent weld quality, faster production times, reduced labor costs, and improved workplace safety..
TIG
Tungsten Inert Gas (TIG) welding, also known as Gas Tungsten Arc Welding (GTAW), is a precision welding process that uses a non-consumable tungsten electrode to produce the weld. An inert gas, typically argon, is used to shield the weld area from atmospheric contamination, ensuring a clean and strong weld. Unlike other welding methods, TIG welding allows for greater control over the weld bead, making it ideal for high-quality, detailed work on thin materials or critical components. This process can be used with or without filler material, depending on the application. TIG welding is commonly used in industries such as aerospace, automotive, piping, and fabrication of stainless steel and non-ferrous metals like aluminum and magnesium.
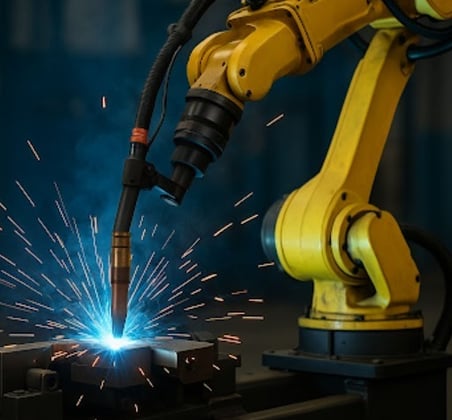
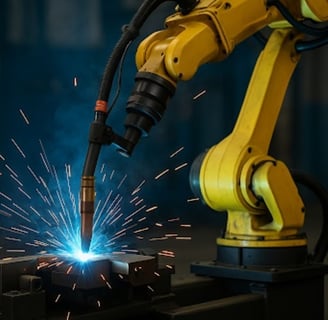
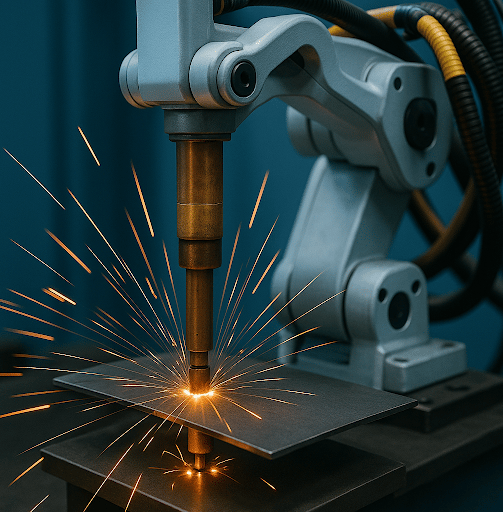
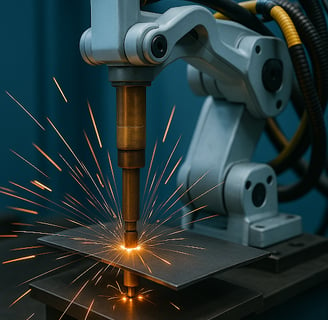
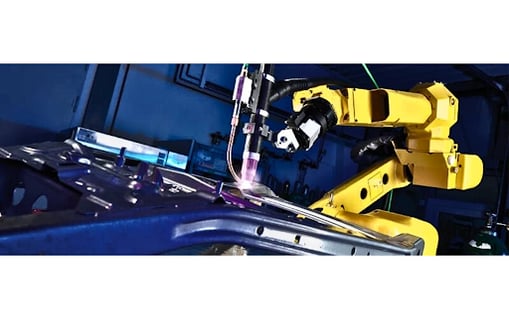
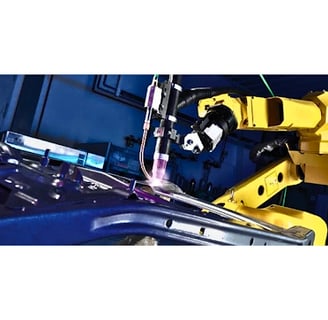
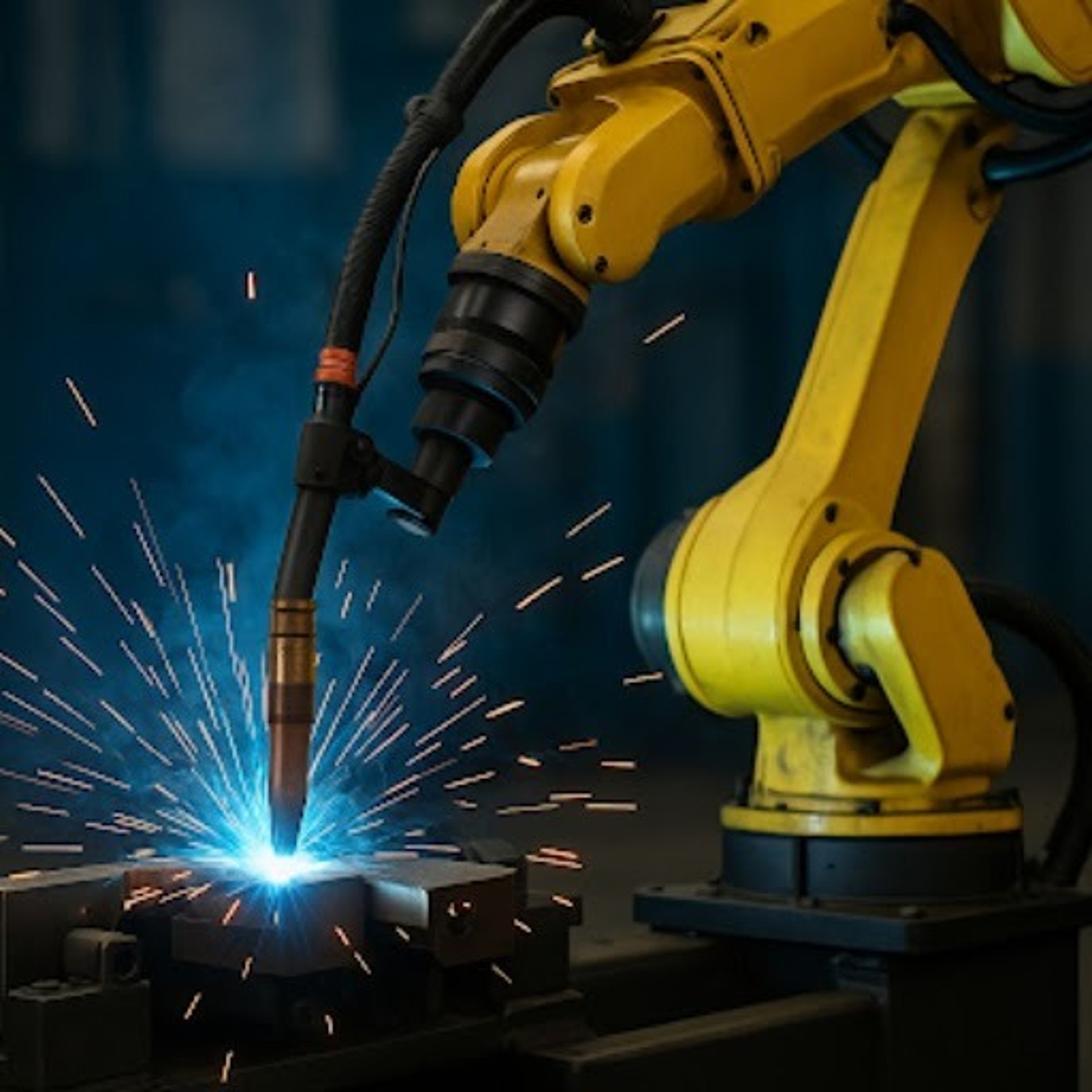
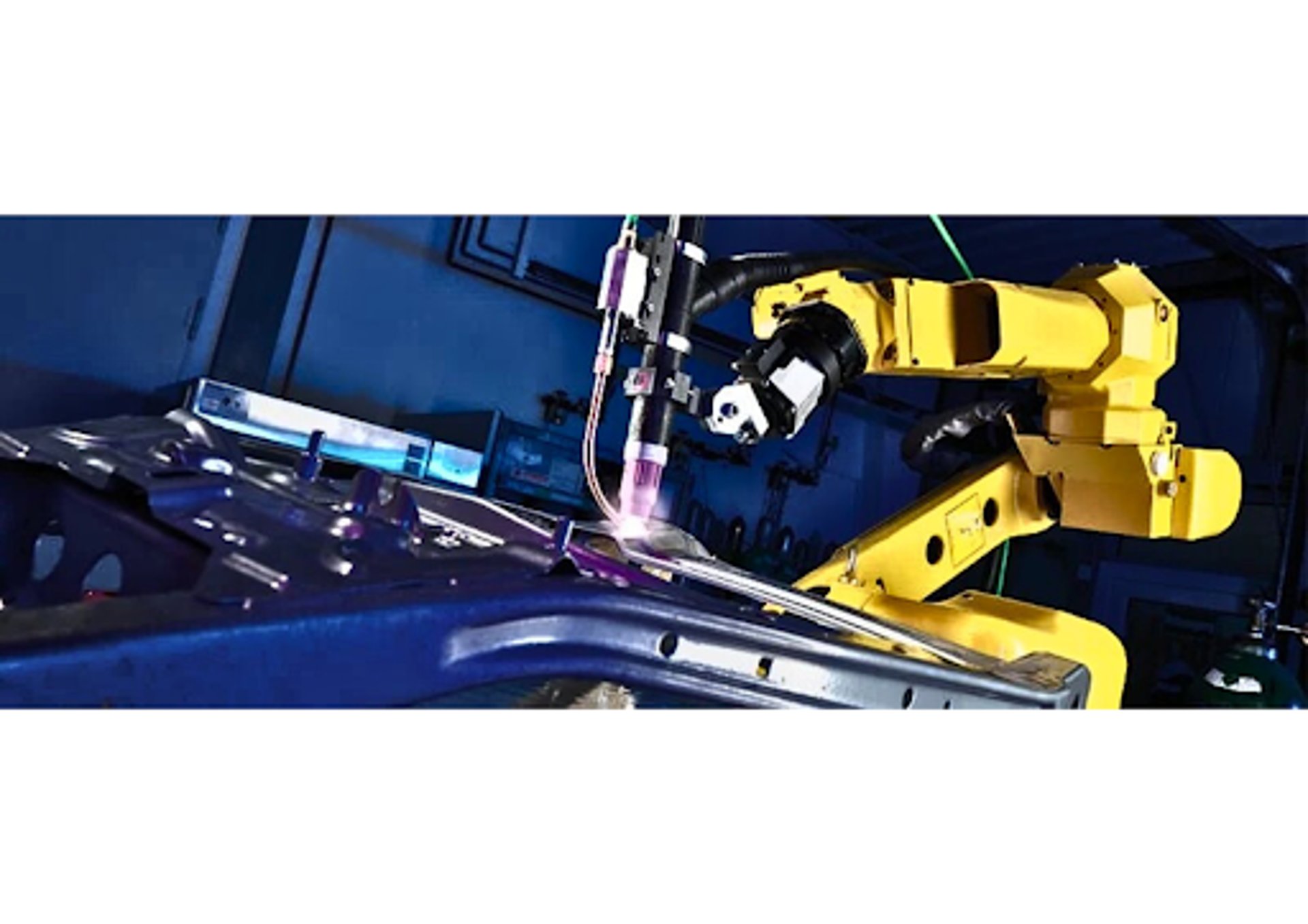
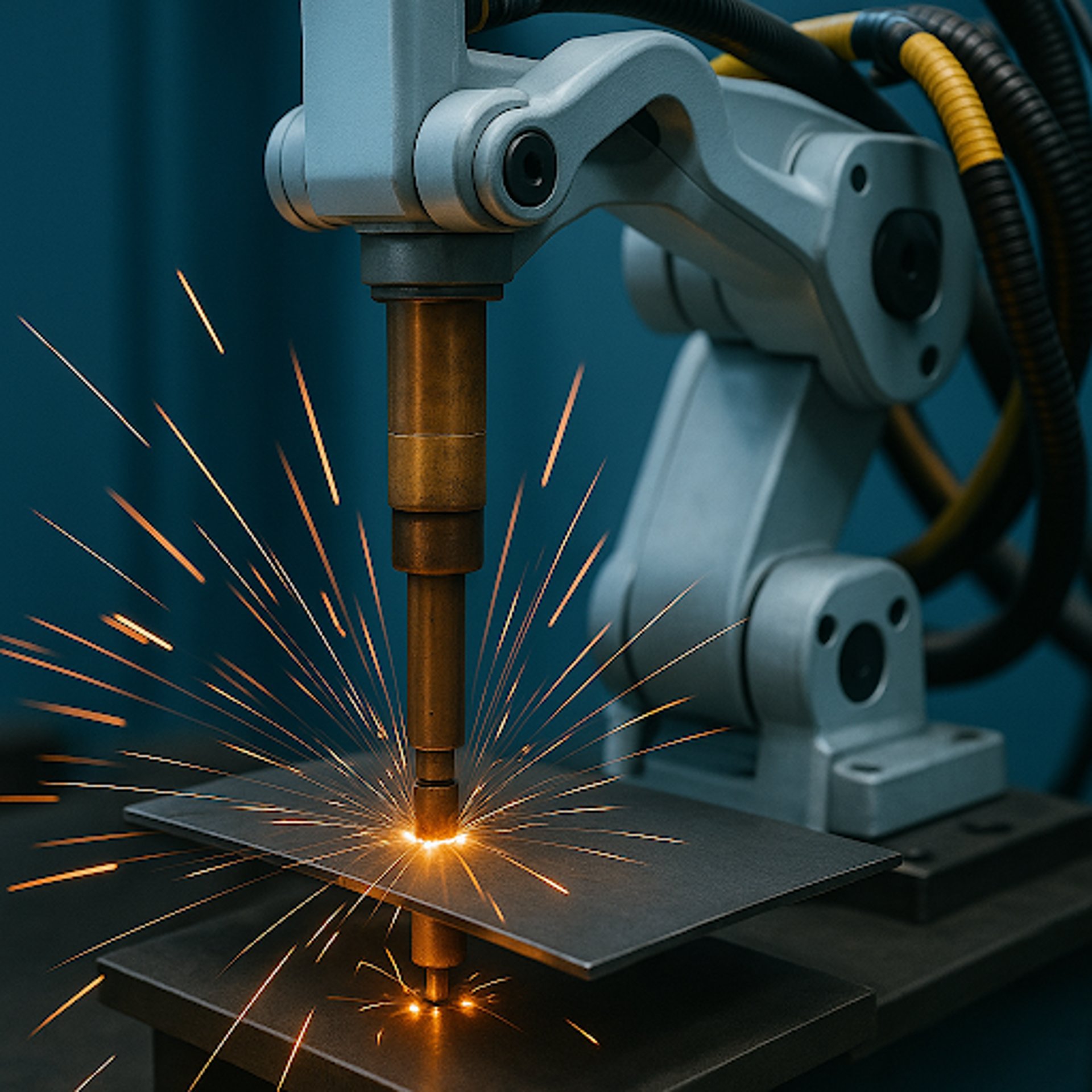